Finnish technology innovation tackles global battery waste: CeLLife launches game-changing upcycling plant
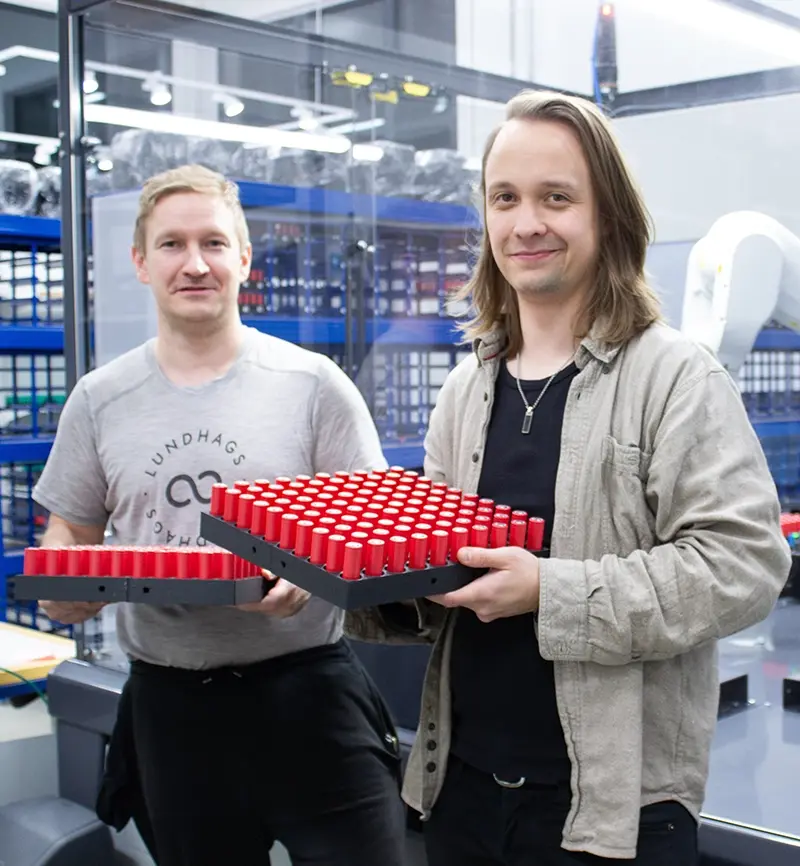
Up to 90% of the battery cells in discarded lithium-ion batteries could be reused, but the lack of rapid and reliable battery cell health testing has been a barrier to reuse. A pilot plant now open in Tampere can measure cells at a rate of one million cells per year. CeLLife Technologies’ patented diagnostic technology can sustainably electrify the world.
The global green transition will require a huge number of lithium-ion batteries. Batteries are not inherently designed to be recycled or reused when they reach the end of their useful life. Battery waste in the European market is expected to grow at a rate of around 20% per year until 2040.
Waste would be reduced if battery cells were recycled, but the key challenge is their non-uniformity – or rather the fact that the condition of battery cells cannot be determined on an industrial scale.
CeLLife has today opened a pilot plant in Tampere, Finland, where mass testing of battery cells can be carried out at record speed and safety.
“The battery industry is in dire need of lifecycle management. Using cells to the end of their useful life is the most sustainable and sensible way to reduce battery waste. There is no sense in the current procedure, which uses heavy chemical processes to separate raw materials or crushes even like-new cells to fill the landfill,” says Marko Tulonen, founder and chairman of the board of CeLLife.
Numerous applications for second-life batteries
CeLLife’s factory will initially process 4,000 to 5,000 battery cells per day, which is many times more than what the big battery companies can do. Thanks to fast and reliable mass testing, up to 90% of the cells of used batteries can be made good as new for the manufacture of batteries. Important application targets for the use of such rechargeable batteries are, for example, 5G network base stations and modular energy storages.
“Here we solve the chicken-and-egg problem: The demand for recycled cells is still low, because accurate, efficient and safe solutions have not yet been available. Everyone needs batteries. A solution has been found. The demand will come to hand explosively within a year or two,” sums up Tulonen.
The factory has approximately 200,000 battery cells in stock, which come from large data centres in southern Finland.
“Some of them have come from backup batteries, which have not necessarily been used at all, but after a couple of years of warranty, these practically new batteries are taken out of service and their fate is to be crushed. There is no need to dig up new lithium, cobalt, manganese, and many other substances from the planet if we can give battery cells a new cycle of use,” says Tuomas Messo, founder and technology director of CeLLife.
At the factory, the cells are tested automatically. When the capacity or charge level of the cell is known, they are sorted with the help of a robot. When rechargeable batteries are assembled from cells of the same condition, their service life can be maximized.
“Here we could use the analogy of a basket of apples, where one bad apple can ruin an otherwise good basket, i.e. the weakest cell determines the quality of the battery. And correspondingly, when the apples are equally fresh, they age in the basket at the same rate,” explains CeLLife founder and CEO Roni Luhtala.
Demand for mass testing at every stage of the value chain
CeLLife also offers mass testing of battery cells as a service. The company already has paying customers at every stage of the battery value chain, from manufacturing to end users and recycling, because the current testing is inefficient and slow.
“Traditionally, in quality control, impedance is only measured at 1-2 points, but the measurements don’t tell anything essential about the cell’s quality, safety and performance. Similarly, it takes up to half an hour to obtain accurate measurement results with traditional methods, which means they are only suitable for laboratory use,” says Luhtala.
CeLLife, on the other hand, measures the impedance of each cell at 2000 different points. The results are obtained in seconds and the measurements give an accurate picture of the condition of the battery and what is the cause of its possible decline in condition. CeLLife talks about the electronic fingerprint of the cells because each cell is an individual. Perhaps the most important part of the diagnosis is an understanding of the battery’s remaining useful life.
Database of over 500,000 cells
What is the diagnosis based on? Research results are mirrored in CeLLife’s database, which is probably one of the largest in the world. It is based on an extensive cell research project started at the University of Tampere in 2010. Over the years, the database has accumulated data from more than half a million cells and it was transferred to the incorporated CeLLife in 2022.
“We compare the measurement data with these previous results and based on this, we can tell about the measurement results and what they mean in practice. Our system scales and learns to be better along the way, while the data collected from the cells is further refined with the help of artificial intelligence,” says Messo.
The technology can be used to test all battery chemistries and models, i.e. there is no need for a separate measuring device for different battery types. The measuring device is light like a tablet, and all measurements use the same database. CeLLife’s technology is extensively internationally patented.
Roots in electrical network diagnostics technology
The roots of the technology of mass battery testing go back to electrical network diagnostics, which Messo and Luhtala have been researching for years at the University of Tampere. In it, the detection of fault situations, their analysis and reaction to them happen elegantly in milliseconds.
CeLLife was founded when they realized that the technology used on the electricity grid side could also be applied to battery testing, where there is a huge demand for reliable and fast solutions.
“Just like in the electricity network, a fault in batteries can also be caused by many reasons. For example, the anode or cathode may have aged or changes may have occurred in the electrolyte that makes it difficult for the lithium ions to travel,” Luhtala illustrates.
Top-level security
In the factory’s process, safety has been taken into account very seriously, because batteries are inherently dangerous.
“Safety is of course based on the fact that we only accept selected cell types to the factory, vague products made in sweatshops are left out by preference. In the process itself, the cells travel on platforms developed for this purpose so that they do not come into contact with each other at any point,” Luhtala describes.
More information:
CEO Roni Luhtala, roni.luhtala@cellife.fi
+358 40 076 4773
Chairman of the board Marko Tulonen, marko.tulonen@cellife.fi
+358 40 508 9848
CeLLife
CeLLife Technologies Oy is a pioneering deep technology startup specializing in advanced diagnostics, measurement, and quality control for the battery industry.
Central to CeLLife’s offering is a patented AI-based Electrical Fingerprint Platform (EFP) measurement technology renowned as the world’s fastest and most accurate. This technology enables swift and precise analysis of battery cells, modules, and systems, providing critical data in seconds.
CeLLife’s innovative approach revolutionizes battery performance assessment and quality control, catering to renewable energy storage, electric vehicles, and portable electronics sectors.
As a pioneer in intelligent and digital battery measurement technology, CeLLife Technologies Ltd is committed to improving the efficiency and safety of battery products with its innovative solutions.
Founded in 2022, the company is headquartered in Tampere, Finland, and is rooted in the extensive research on rapid measurement technologies conducted at Tampere University.