Ensure production quality
Industrial Automation Companies and System Integrators
Gain performance certainty
Improve cost efficiency and sustainability
Overcoming stock quality assurance issues
Managing large quality assurance programs to gain certainty is incredibly time-consuming and a delay-prone phase in the battery product launch, wasting numerous hours on manual work every week.
Managing large-scale entry quality test programs to ensure supplier's cell quality is incredibly time-consuming. Therefore, battery assemblers have been relying on the quality assurances of their suppliers, which is risky due to inconsistent production quality.
Consistency in battery pack quality is a major challenge, just as it is in battery cell manufacturing. The quality of the overall battery pack is determined by the weakest cell. Ensuring that each cell meets high-quality standards requires thorough and accurate testing methods. Variability in cell quality in assembled module/pack can lead to performance and reliability issues, and in the worst cases, to reputational and financial problems. High quality assurance requires testing both before and after assembly at the cell and module levels.
Battery and battery cell quality testing traditionally consumes a substantial amount of time and resources. Manual data analysis, often required for each test, can take up to dozens of hours, delaying the product delivery and occupying valuable human resources. This inefficiency not only stretches timelines but also diverts resources from other critical areas such as research and development.
Detecting defects early in the assembly process is crucial to avoid defective products reaching the market. However, traditional testing methods may not identify issues until late in the process, leading to increased waste and costs. Early detection allows for immediate corrective actions, minimizing scrap rates and maintaining high-quality standards. This is essential to reduce the risk of costly returns and recalls, which can damage revenue and brand reputation.
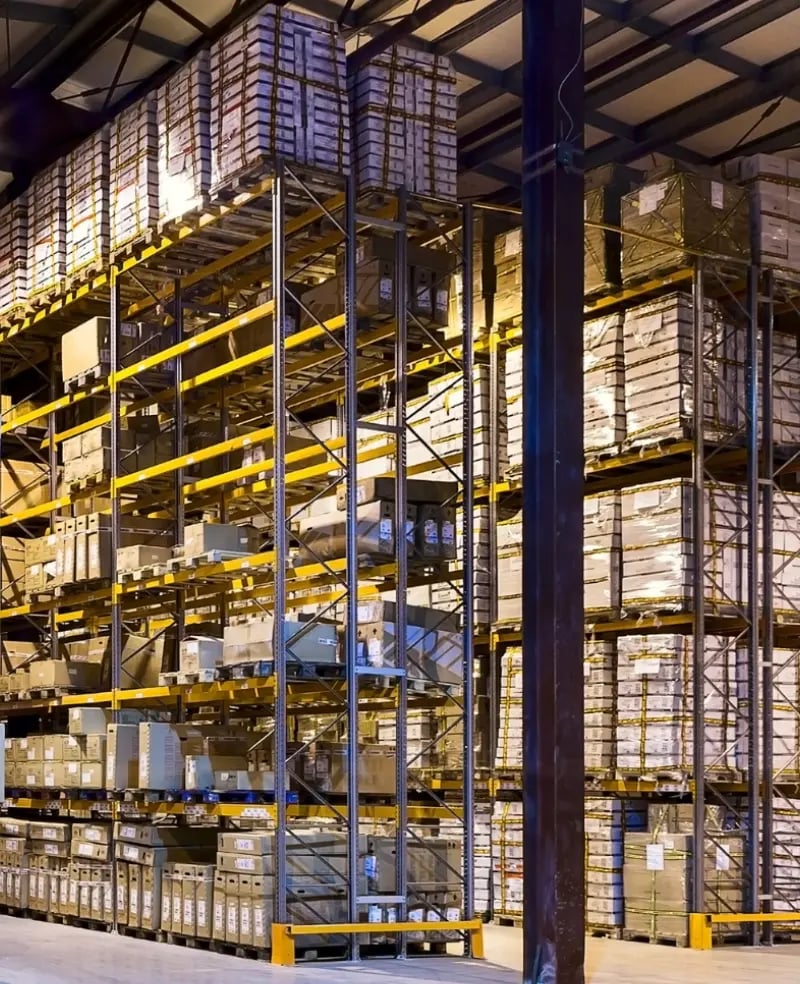
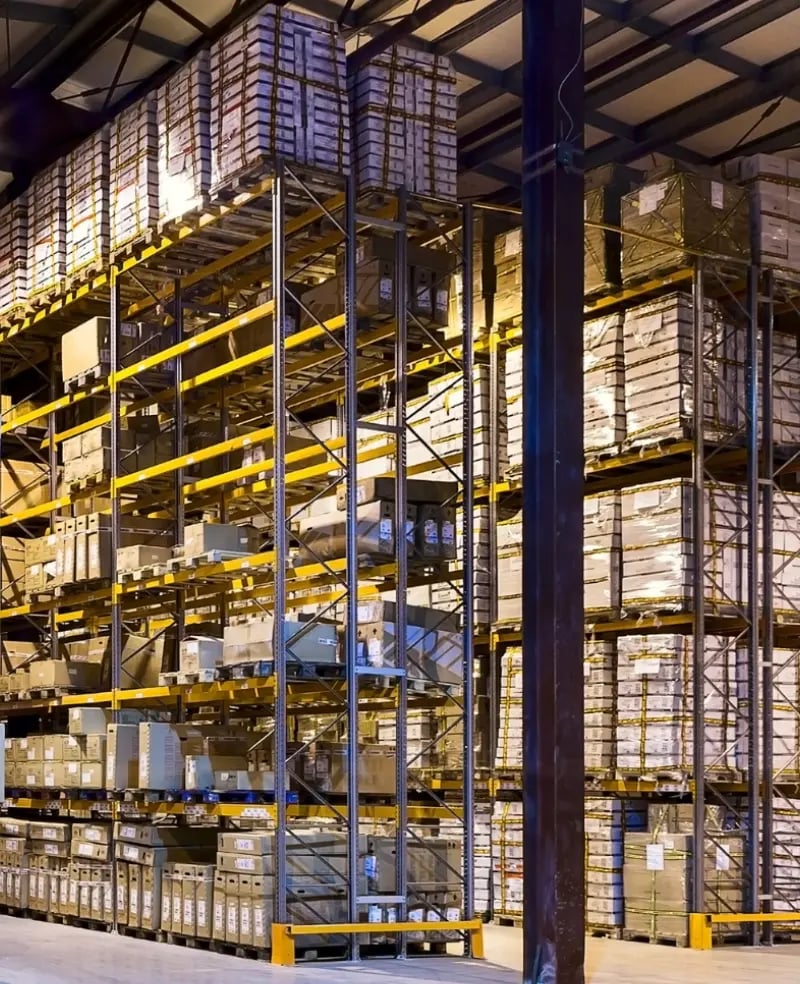
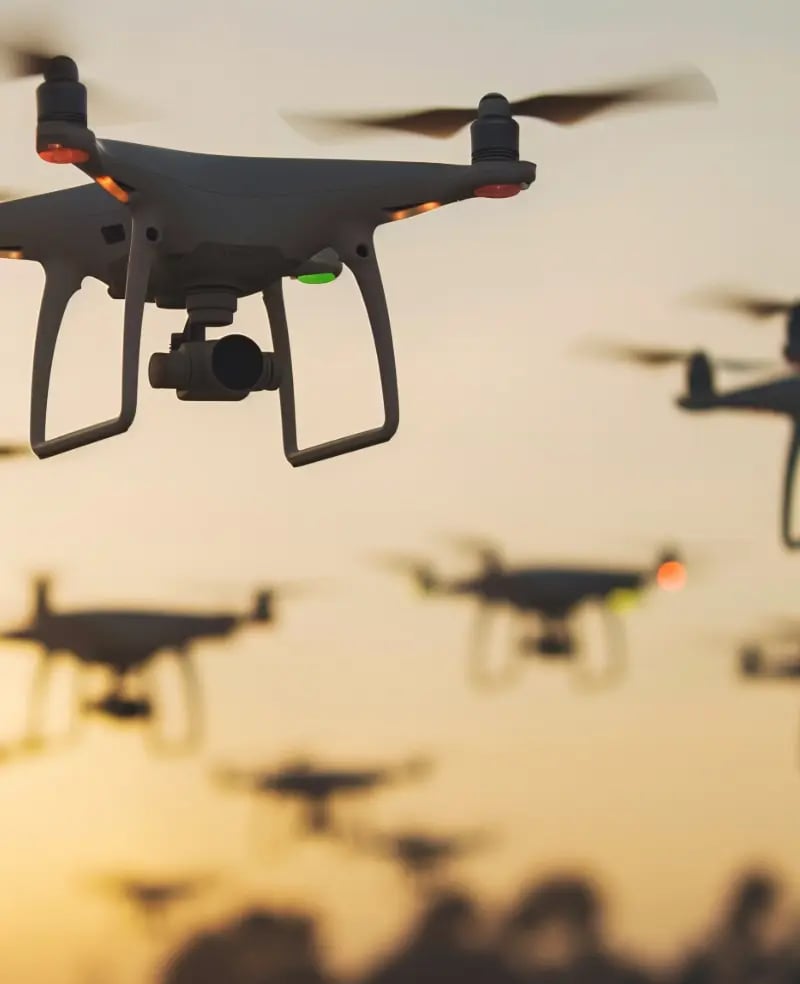
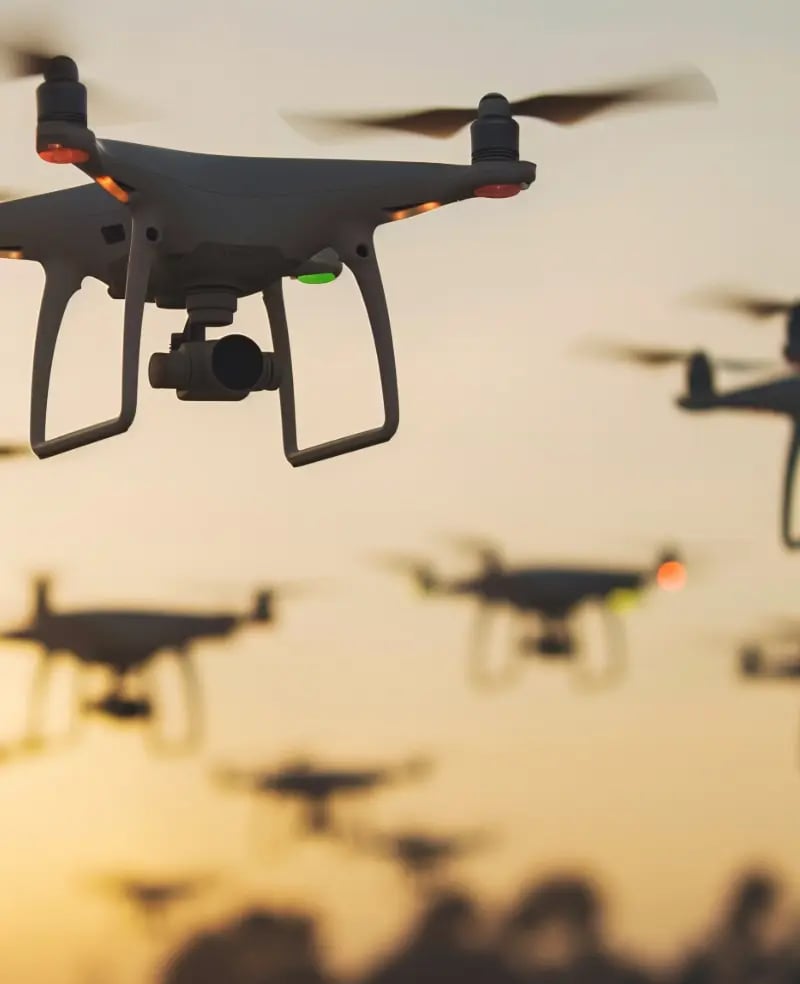
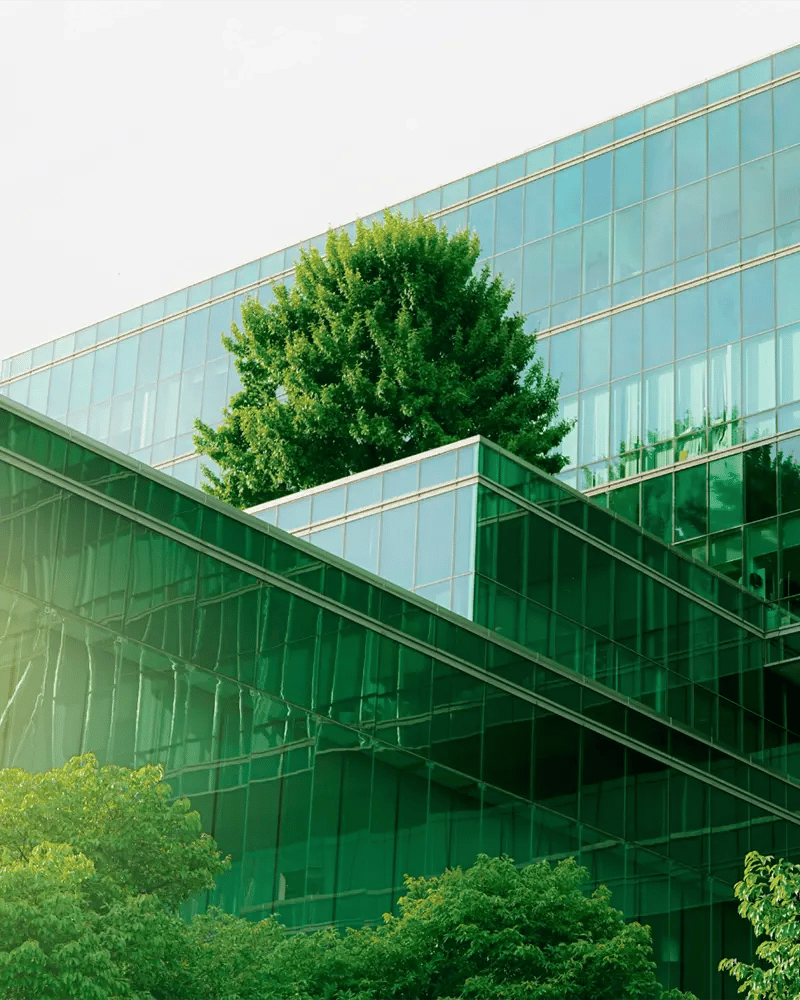
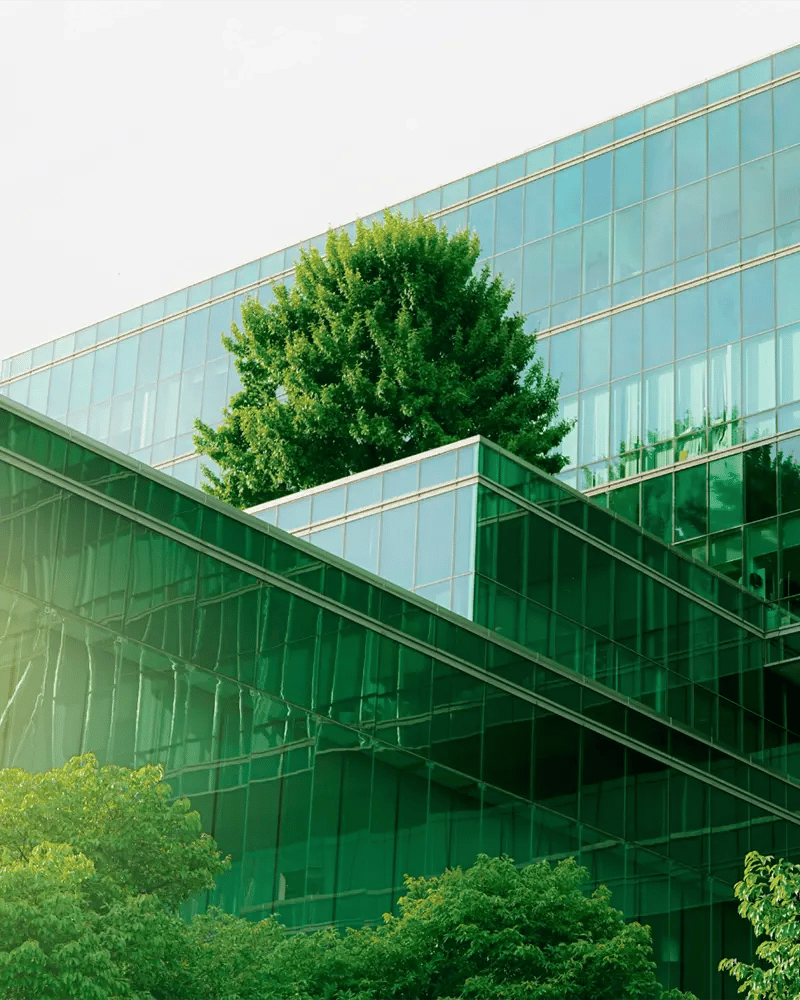
What CeLLife can provide to you
Speed
Measurement results in seconds, not hours. Test hundreds of cells and modules while traditional methods would still be processing the first.
Accuracy
Laboratory grade accuracy, delivers over 2,000 data points in under 2 seconds, which is hundreds times faster than other methods.
Data & analytics
All essential data, comprehensive insights, and analytics are in the cloud, enabling informed decision-making in real-time.
Modifiability
For all cell and battery chemistries and types, from battery modules and packs to supercapacitors and fuel cells.
CeLLife use cases for battery assembling
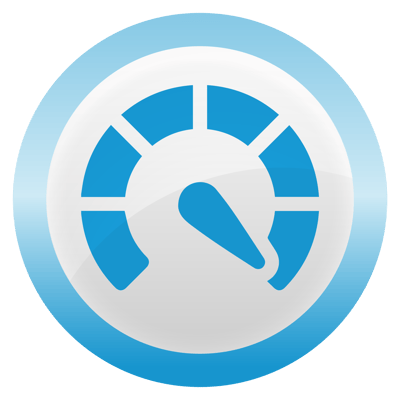
Validation of supplier quality
Gain full coverage for entry check and ensure certainty of the supplier quality. Compare and validate electrical data that manufacturer provides with EFP-measurements.
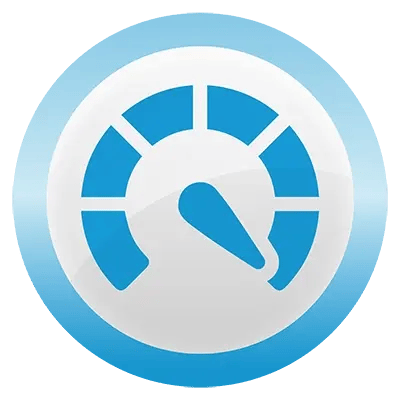
Testing and measurement
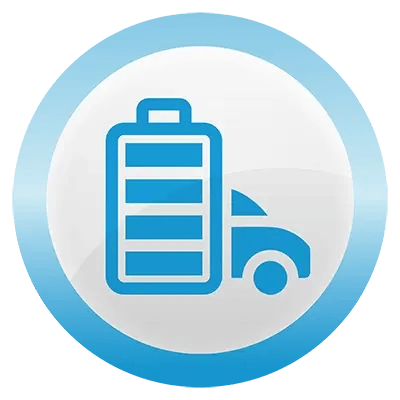
Grading and characterization
Quickly grade the quality of the cells beyond good/bad categorizations. Identify cell-to-cell variations in incoming cells and assemble modules with homogeneous quality, ensuring certainty in battery quality.
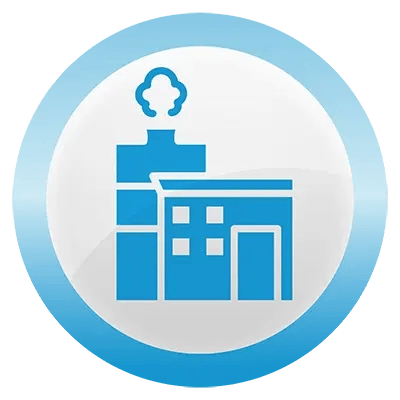
Quality control and defect detection
Save money and detect defects early in the production process. Identify issues in electrochemical properties and, for example, welding issues inside the cell and module.
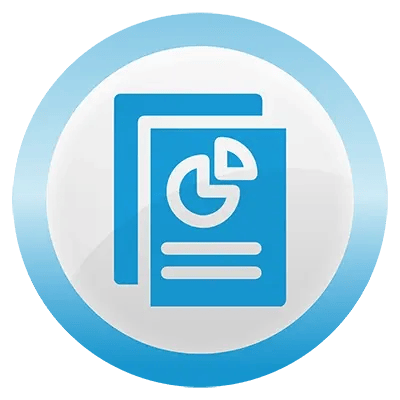
Data mining and analytics
Seamlessly access comprehensive insights and analytics, empowering traceability for root-cause analysis and data-driven decision-making in real-time.
Benefits of CeLLife for battery assemblers
CeLLife's advanced technology significantly benefits battery assemblers by addressing critical quality assurance issues in the assembly process. Ensuring consistency and quality across battery cells is a major challenge, as the overall performance and reliability of battery packs are determined by the weakest cell. CeLLife’s Electrical Fingerprint Platform (EFP) mitigates these risks by providing rapid, reliable measurements in seconds, allowing assemblers to measure every cell during and after entry checks, and all the produced batteries. By testing and identifying each cell and later the module, you gain traceability for the entire module and its cells, as well as better condition analysis throughout its entire lifecycle. This substantial increase in testing speed enhances efficiency, enabling companies to meet market demands more effectively.
In addition to speed, CeLLife’s technology delivers laboratory-grade accuracy by analyzing over 2,000 data points in 2 seconds. This precision ensures early detection of defects, allowing for immediate corrective actions that reduce waste and production costs. Early defect detection not only minimizes scrap rates but also ensures that only high-quality cells are used in battery packs.
CeLLife’s platform also excels in providing comprehensive data and analytics. The platform ensures comprehensive traceability by maintaining uniform electrical measurements for every cell, storing all data for further analysis, and tracing back potential quality issues to their root causes. With CeLLife manufacturers gain real-time insights that drive informed decision-making. This data-driven approach enables continuous optimization of production processes, leading to higher operational efficiency and consistent product quality. The platform's adaptability to various battery chemistries reduces the need for multiple testing systems.
Moreover, CeLLife empowers battery pack assemblers with advanced tools for quality control and defect detection. It enables achieving full coverage in measuring every cell during entry checks, ensuring comprehensive quality control, accurate anomaly detection, and efficient provisioning. The EFP measurements provide a detailed electrical analysis, issue detection, and data-based grading without user subjectivity. This ensures that battery modules are assembled with uniform quality and that all cells meet high-quality standards before and after module assembly, enhancing overall reliability and customer satisfaction. By integrating CeLLife’s innovative solutions, battery assemblers can achieve a sustainable competitive advantage through enhanced efficiency, reduced costs, and superior product quality.
Concrete example of CeLLife's benefits for defence industry
Entities with thousands of batteries must rely on accurate condition assessments to guarantee operational safety. CeLLife’s technology allows customers to quickly grade their batteries, optimizing their usage and enhancing operational efficiency. For example, a company previously spent 6 hours checking the condition of a single battery. With CeLLife, they can now analyze thousands of batteries in the same time frame, gaining cell-level insights from each battery. This drastic improvement saves time and resources to ensure the reliability and safety of their operations.
.png?width=2000&height=1414&name=Untitled-36%20(14).png)